数控加工产品设计从CAD文件开始,以获得可制造的加工零件。这些CAD文件应该遵循特定的加工设计指南。使用DFM策略从一开始就减少了加工设计中可能出现的问题,节省了时间和金钱。
数控加工的DFM分析可以在CAD文件上运行,以找出任何可能的设计问题,例如小孔和深孔、非标准半径地板圆角等。分析的结果将发现不符合DFM检查标准的零件特征。
铣削
数控铣削是指从原材料中快速减去材料,直到达到所需的形状的加工过程。铣削由圆形刀具(最常见的是立铣刀)进行,这些刀具以浅切深度将材料从旁边削掉。在设计零件时,请记住数控铣削常用的工具类型。如果您能够使用标准工具实现所需的功能和几何形状,您可以降低成本和交货时间。否则,制造商将不得不花费时间和金钱来采购或制造专用工具。
钻孔
钻孔是指在一块材料上打孔的操作。钻孔工具专为垂直切割而设计,并具有圆锥形尖端,允许它们深入材料中。
车削
数控车削是一种制造工艺,其中将材料棒固定在卡盘中并旋转,同时将工具送入工件上,以去除材料以创造所需的形状。在车削操作中,设计零件便于固定和牢固固定。避免在切割工具中需要尖角和尖尖的设计,因为这些会使工具更容易损坏。最好避免中断切割,因为它们往往会缩短工具寿命。
铣削问题
深腔
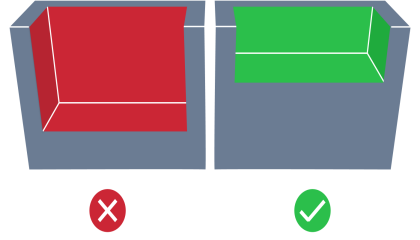
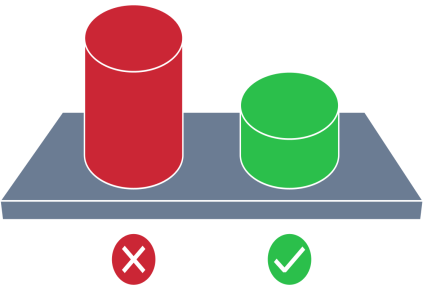
高凸起
大型铣削零件
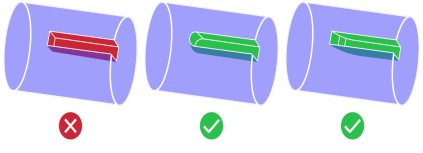
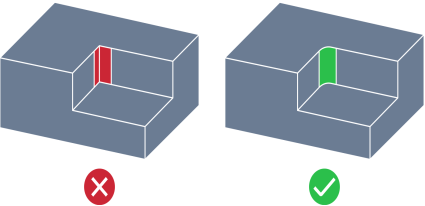
小半径内部角
非垂直铣削零件形状
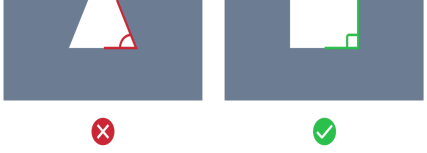
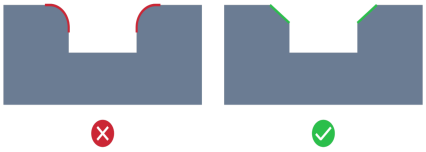
外部边缘圆角
非标准半径地板圆角
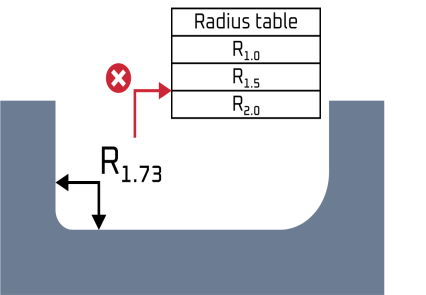
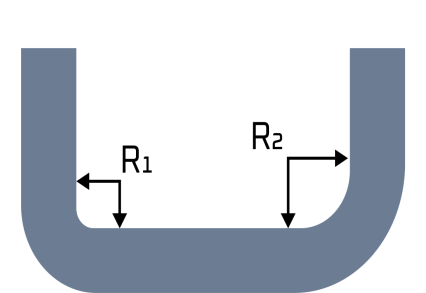
半径不一致的地板圆角
深腔中的狭窄区域
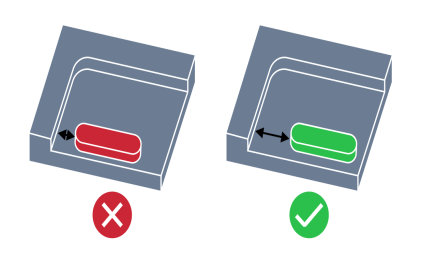
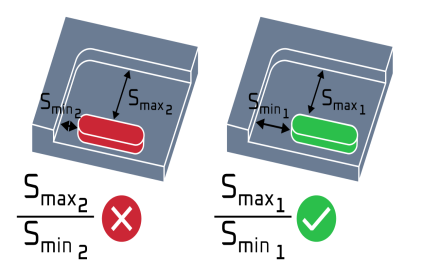
口袋中区域大小差异很大
壁厚小
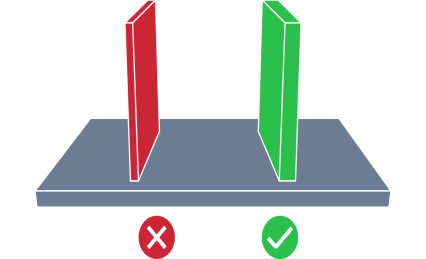
钻孔问题
小孔直径
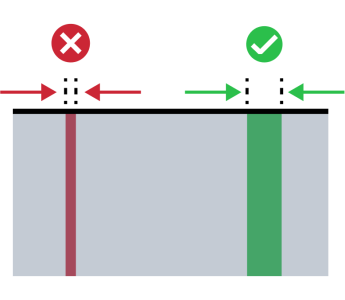
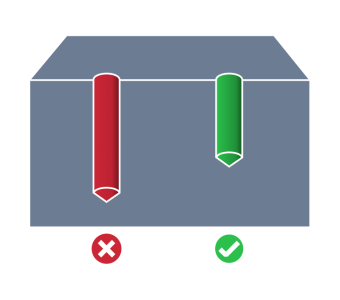
深洞
平底孔
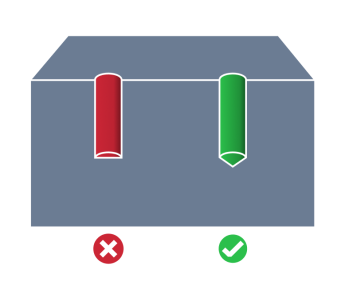
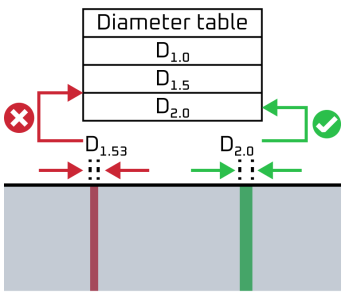
非标准孔
非标准钻点角度
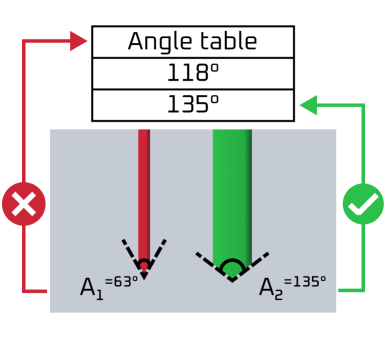
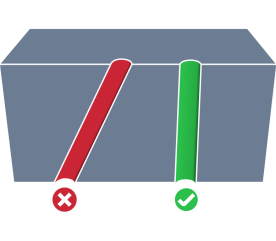
非垂直孔
交叉腔孔
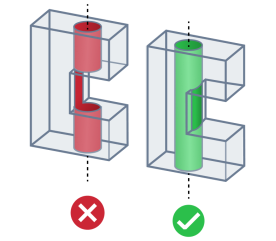
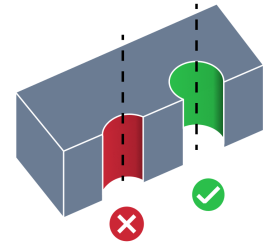
不完整孔
车销问题
深钻孔
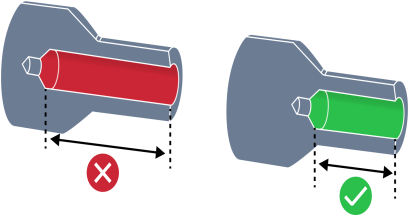
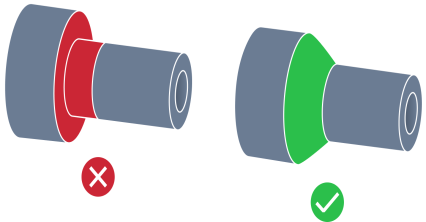
不规则外径轮廓浮雕
大型车削零件
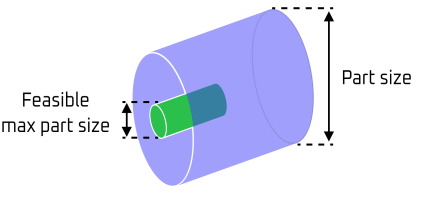
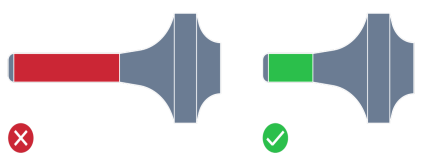
长而细的车削零件
小深度盲孔浮雕
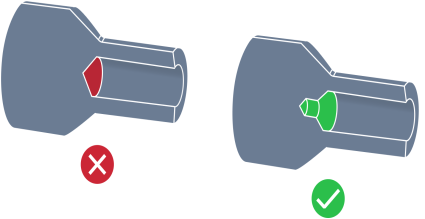
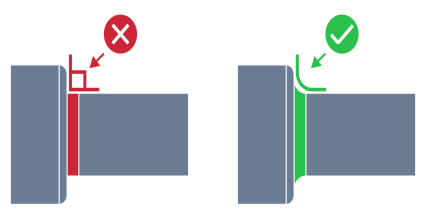
小半径内部角
方形端键
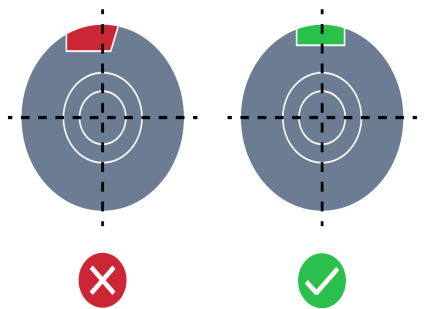
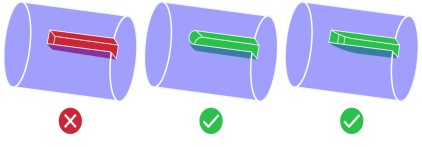